meblowych
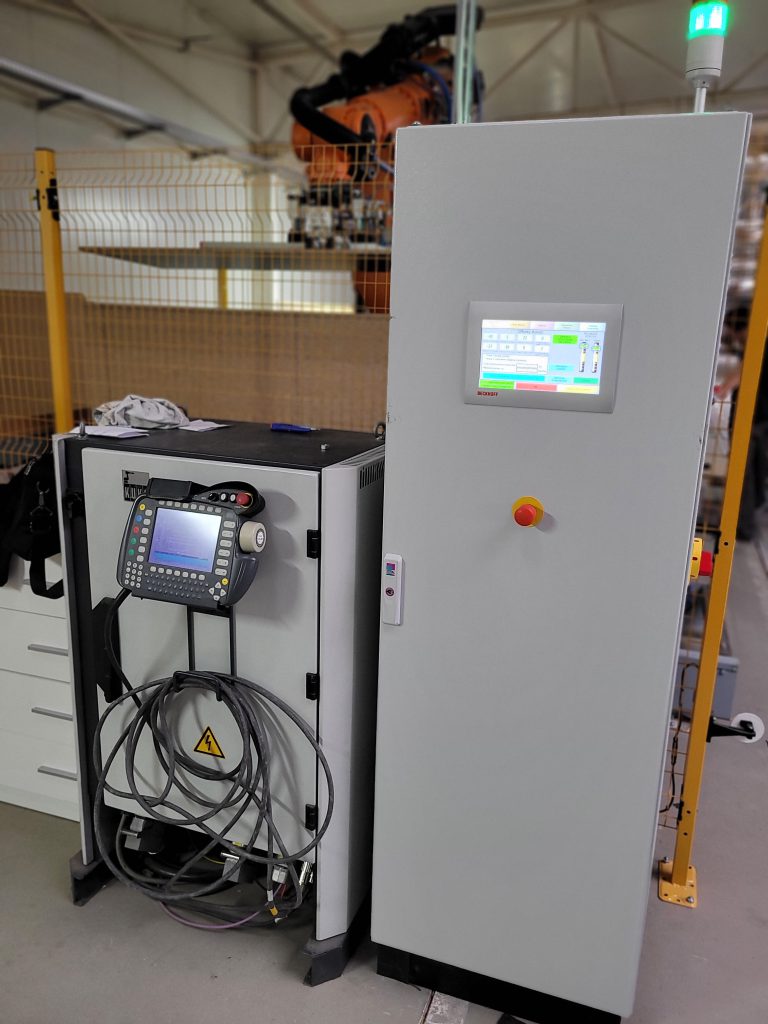
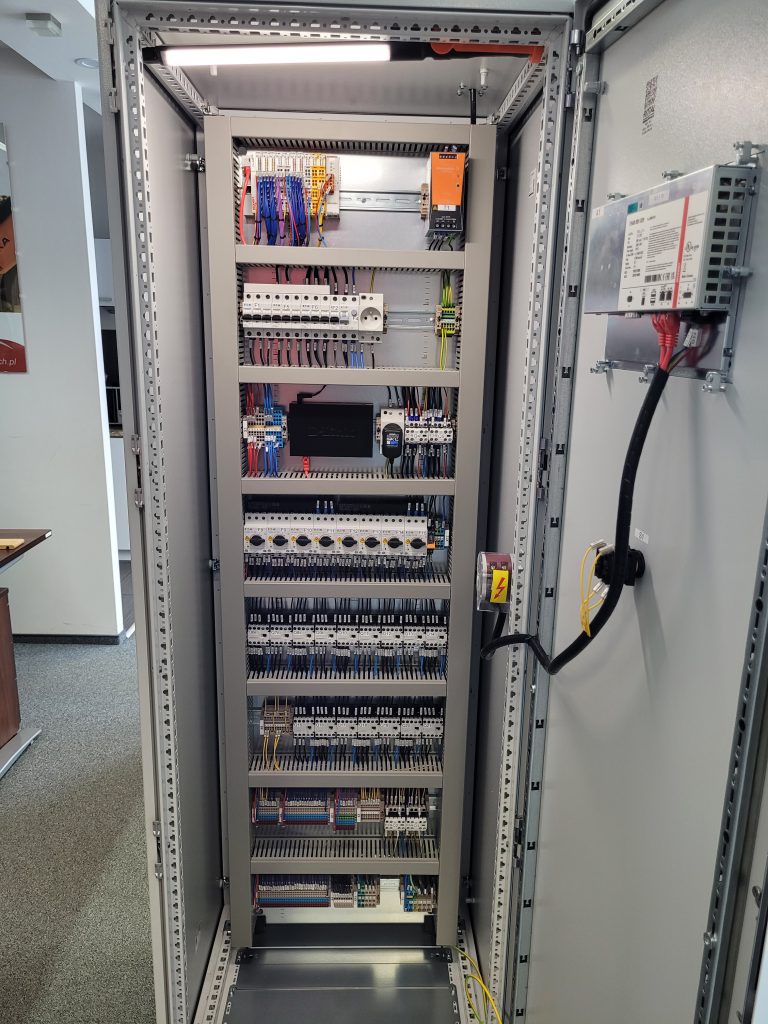
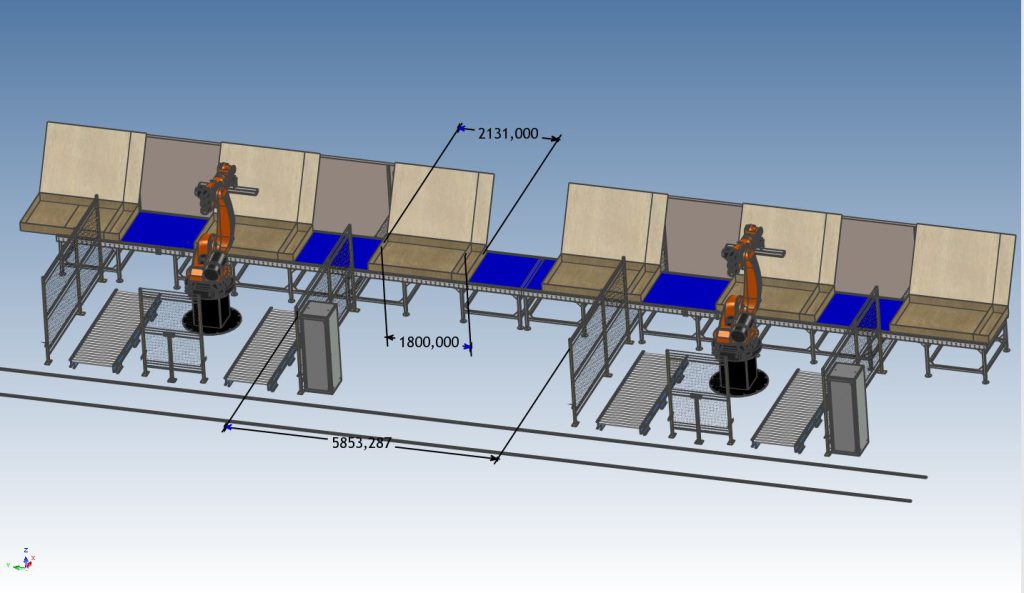
Projekt i wykonanie linii odpowiedzialnej za konfekcjonowanie gotowych płyt meblowych. Za pomocą czujników odległości robot mierzy geometrię palety, pobiera element i automatycznie odkłada odpowiednio zorientowaną w przestrzeni płytę do kartonu. Stanowiska pozwalają na pobieranie materiału w różnych układach (1x1, 2x1, 1x2, 2x2) oraz na pobieranie naprzemienne z dwóch transporterów (lewa-prawa strona). Roboty mogą pracować jednocześnie oraz niezależnie w zależności od zapotrzebowania i asortymentu. W ramach prac:
- Przygotowano koncepcję stanowiska oraz wykonano porojekt 3D,
- Wykonano schemat AKPiA wraz z wyspecyfikowaniem elementów automatyki,
- Wykonano szafę sterującą,
- Wykonano kompleksowe narzędzie do sterowania stanowiskiem za pomocą przyjaznej wizualizacji HMI,
- Przeprowadzono prace elektryczne przy montażu szafy AKPiA, silników, czujników, zaworów oraz dodatkowych urządzeń wykonawczych,
- Przygotowano listę alarmów oraz połączenie zdalne w celu łatwej diagnostyki procesu,
- Przeprowadzono uruchomienie wraz z testami układu sterowania,
- Przeszkolono zespół operatorów odpowiedzialnych za pracę przy maszynie.
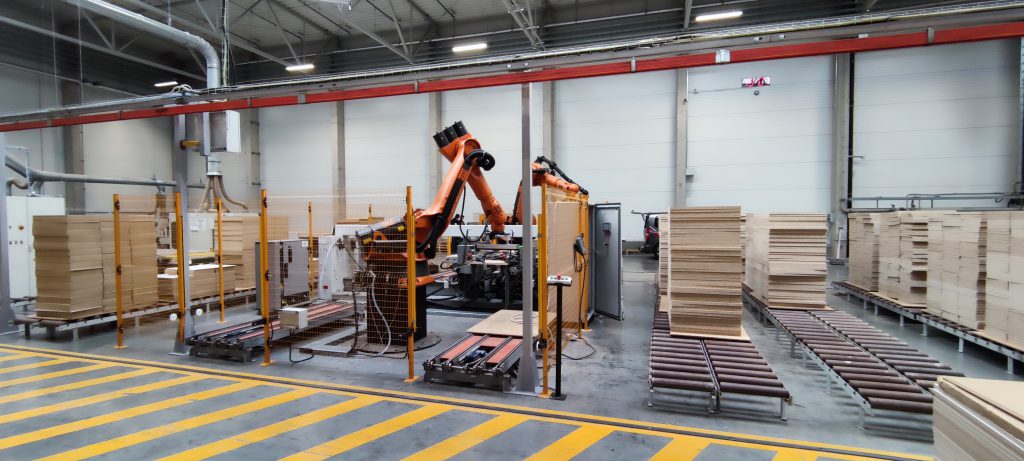
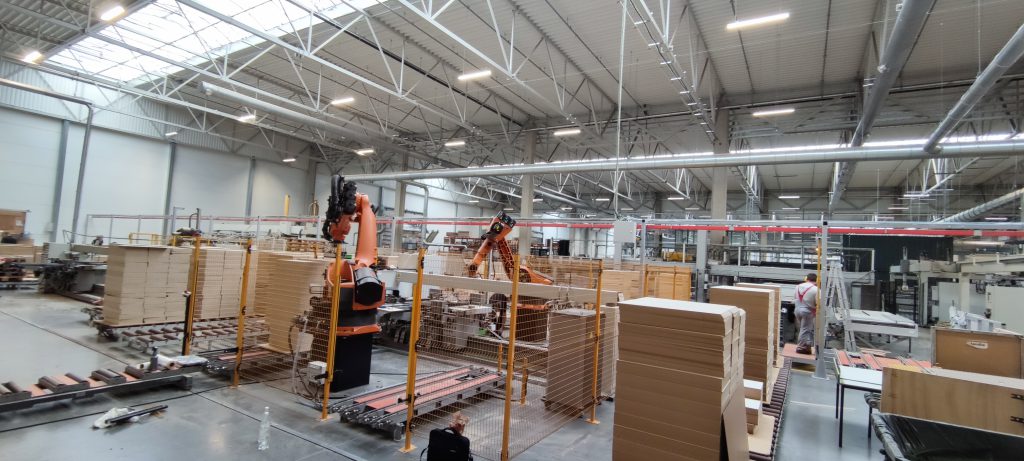
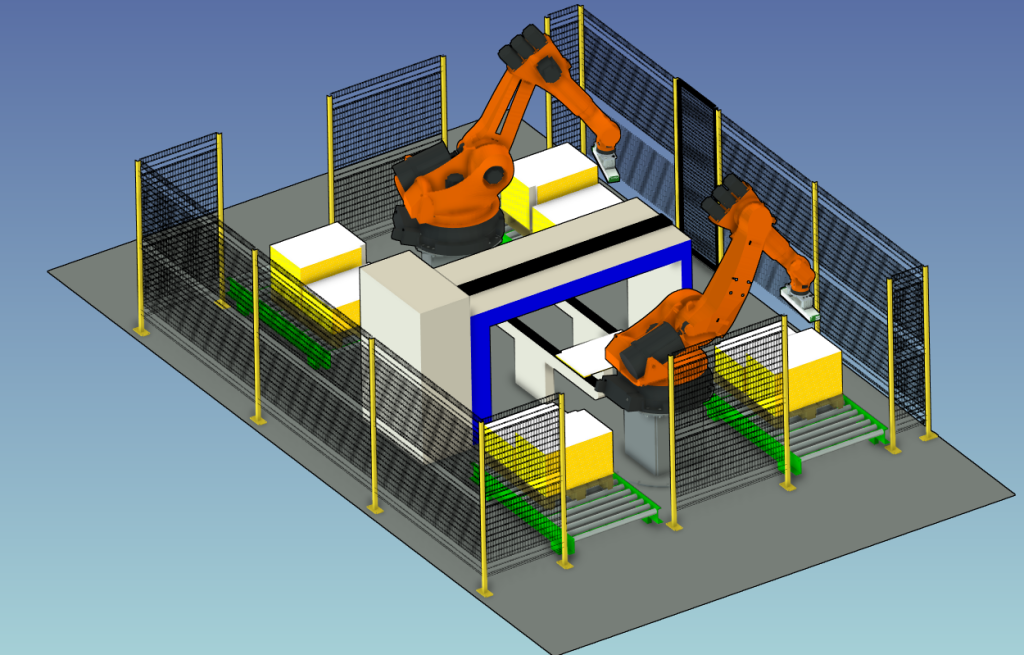
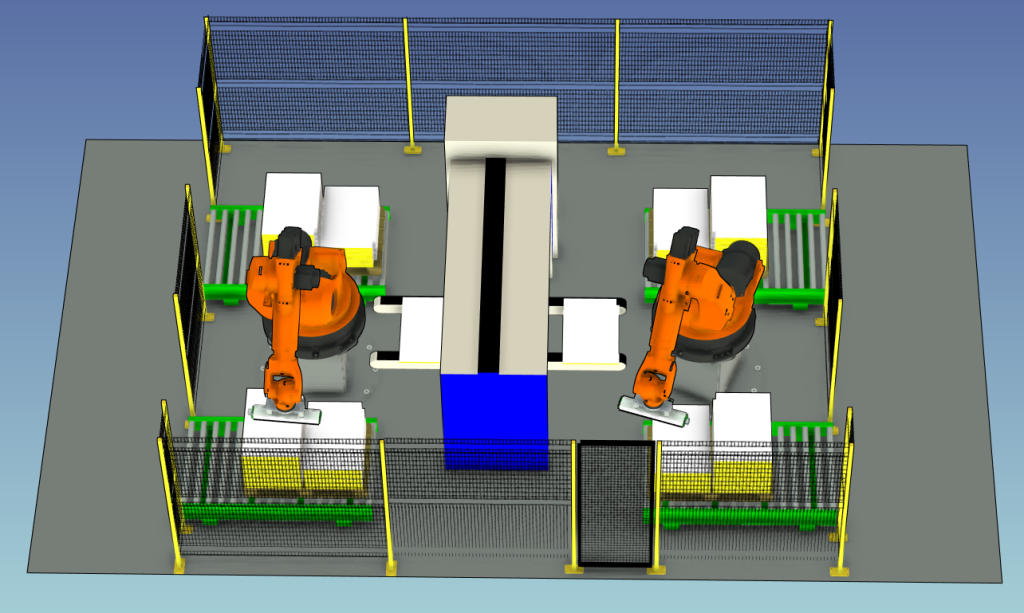
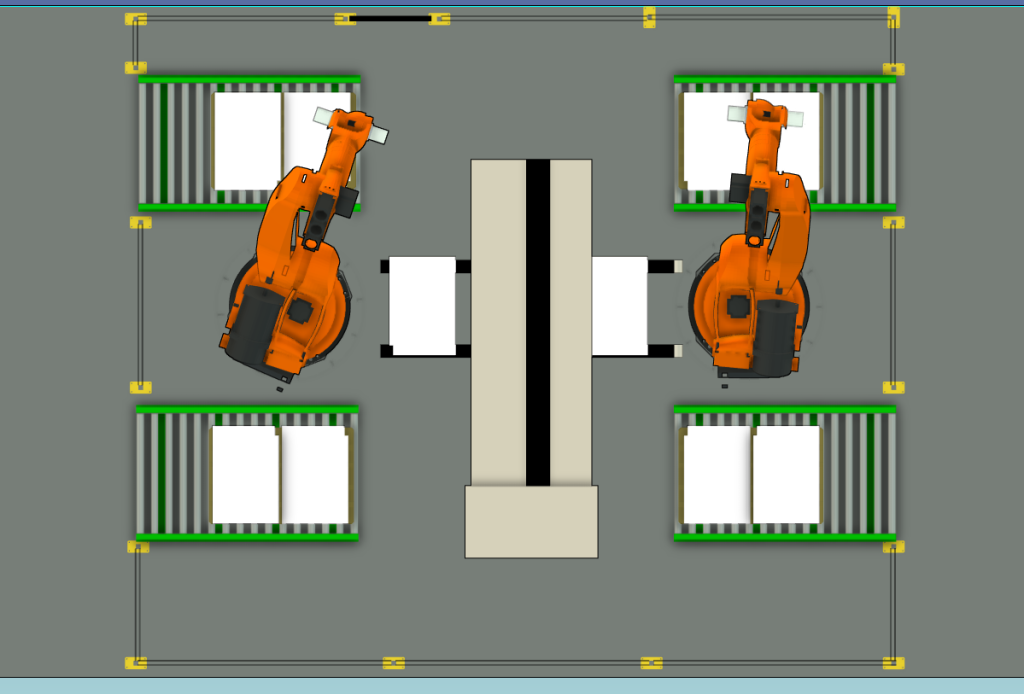
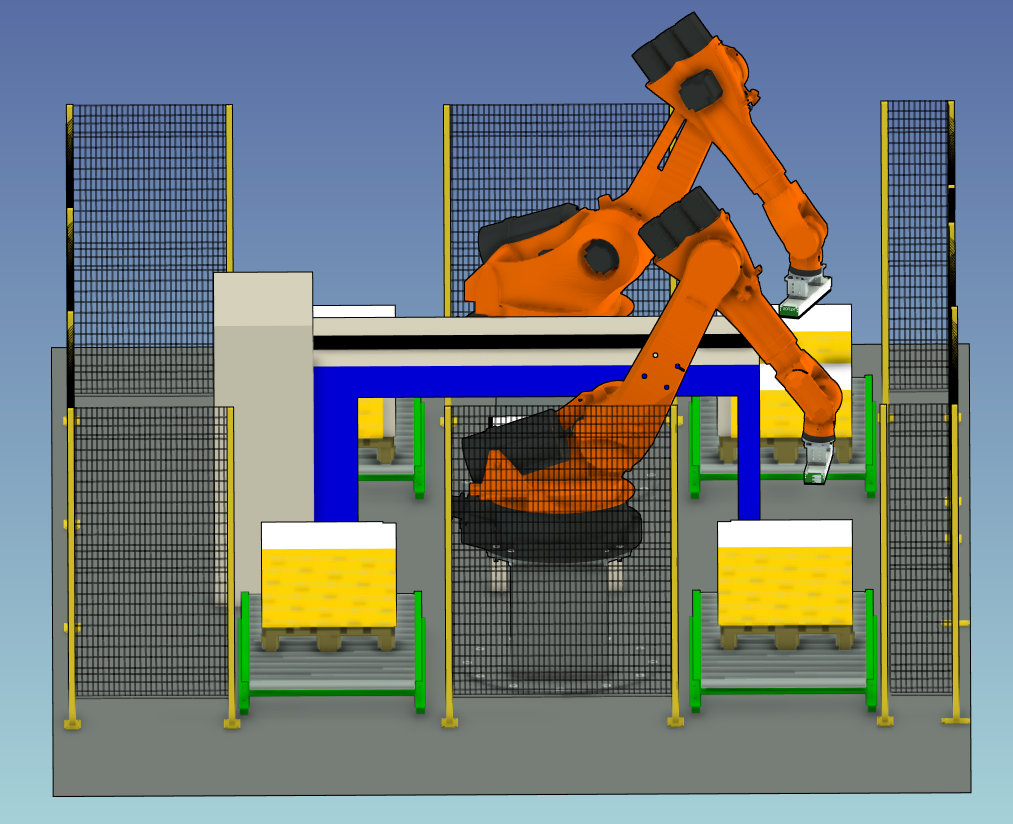
- Przygotowano koncepcję stanowiska załadunkowo-rozładunkowego,
- Wykonano projekt CAD stanowiska,
- Wykonano schemat AKPiA wraz z wyspecyfikowaniem elementów automatyki,
- Wykonano szafę sterującą,
- Zaprojektowano kompleksowe narzędzie do sterowania stanowiskiem za pomocą przyjaznej wizualizacji SCADA,
- Przygotowano listę alarmów oraz połączenie zdalne w celu łatwej diagnostyki procesu,
- Przeprowadzono prace elektryczne przy montażu szafy AKPiA, silników, czujników, zaworów oraz dodatkowych urządzeń wykonawczych,
- Przeprowadzono uruchomienie wraz z testami układu sterowania,
- Przeszkolono zespół operatorów odpowiedzialnych za pracę przy maszynie.
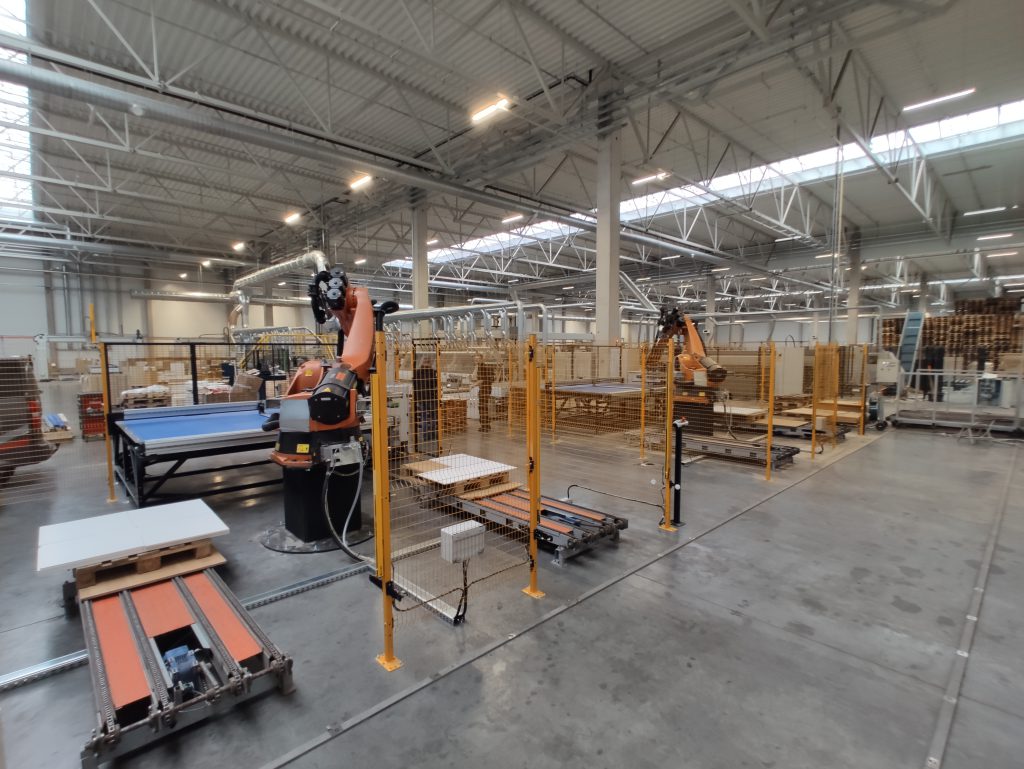

i rozładunek za pomocą robotą
KUKA KRC2
i rozładunkowe
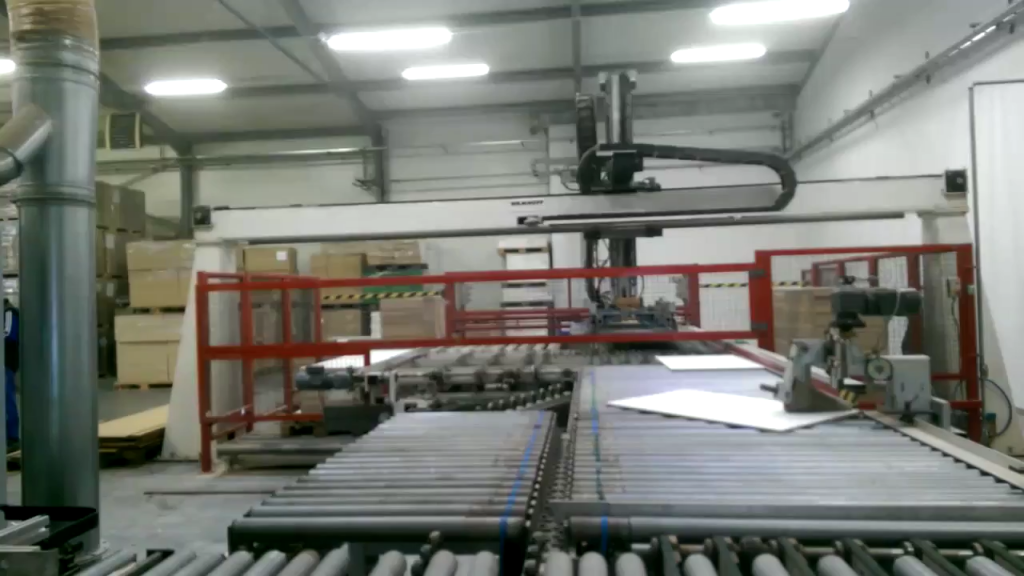
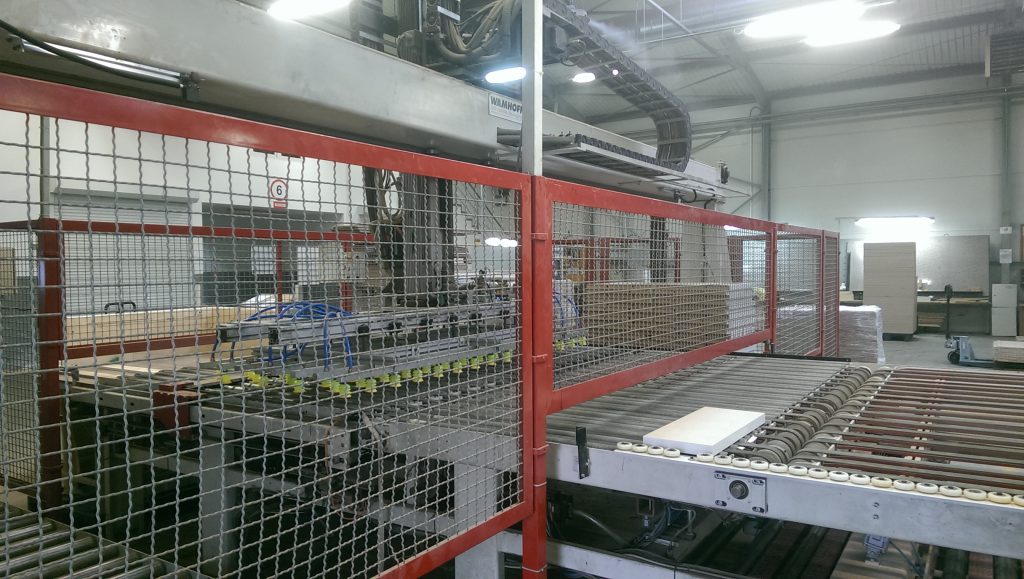
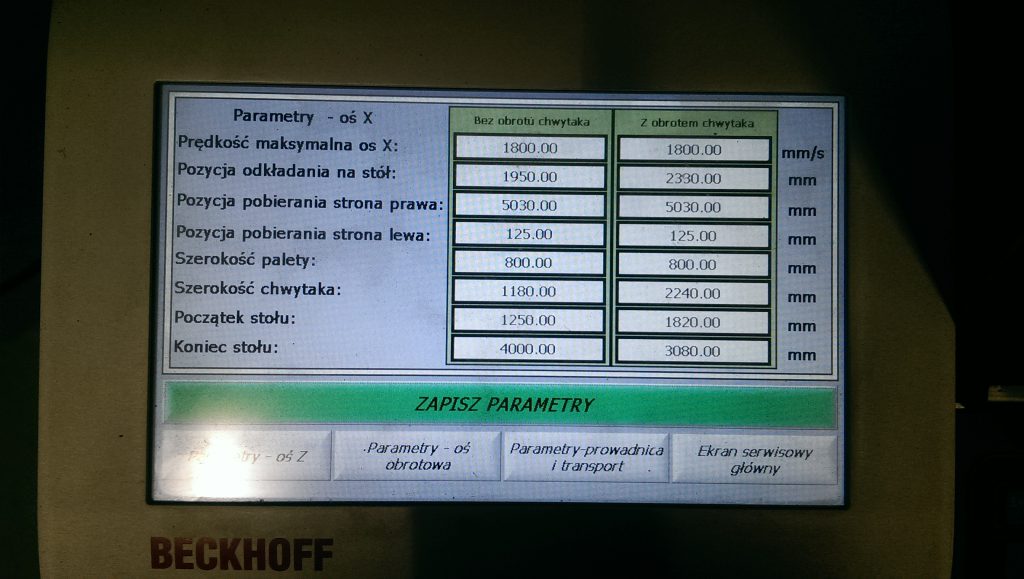
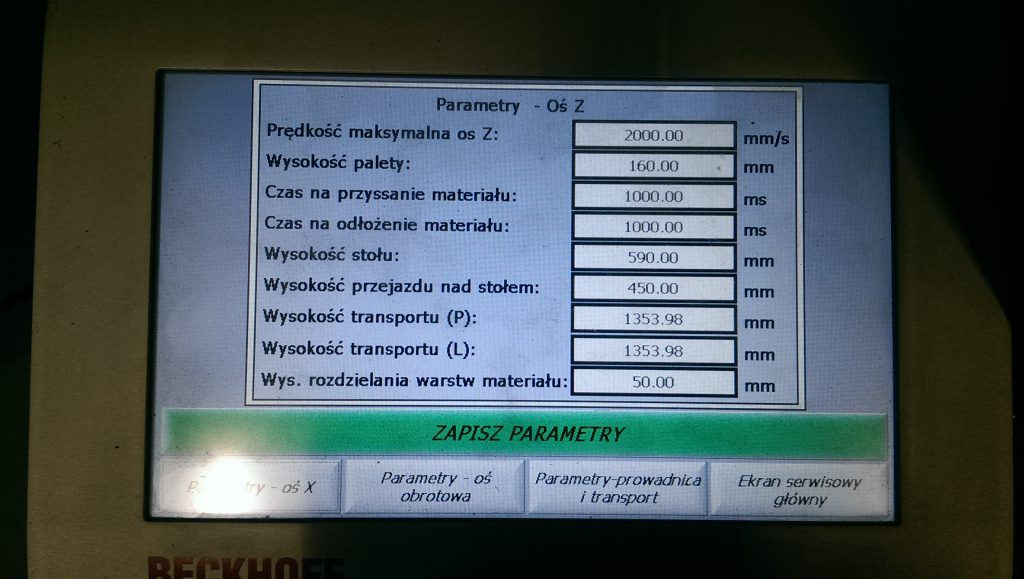
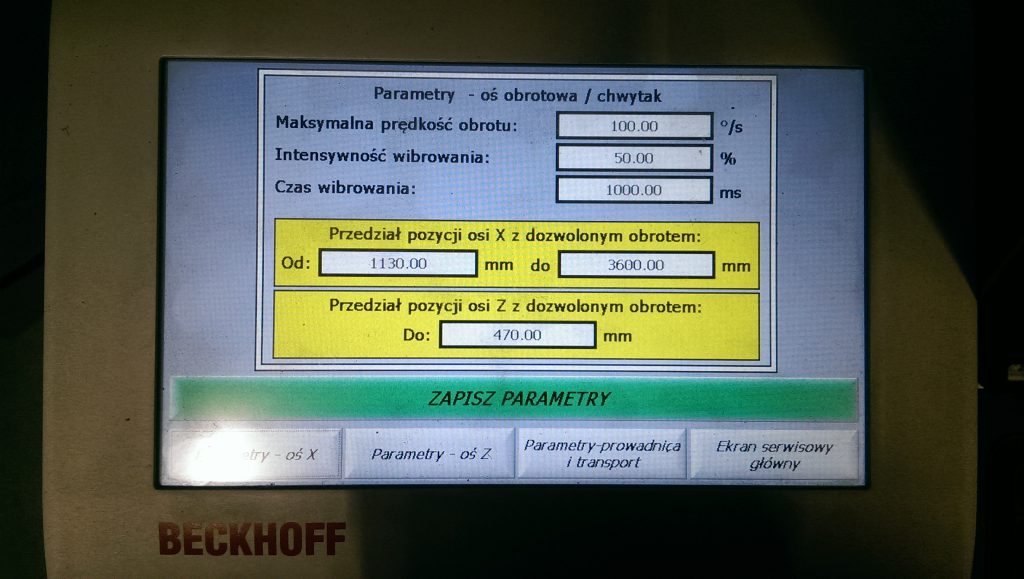
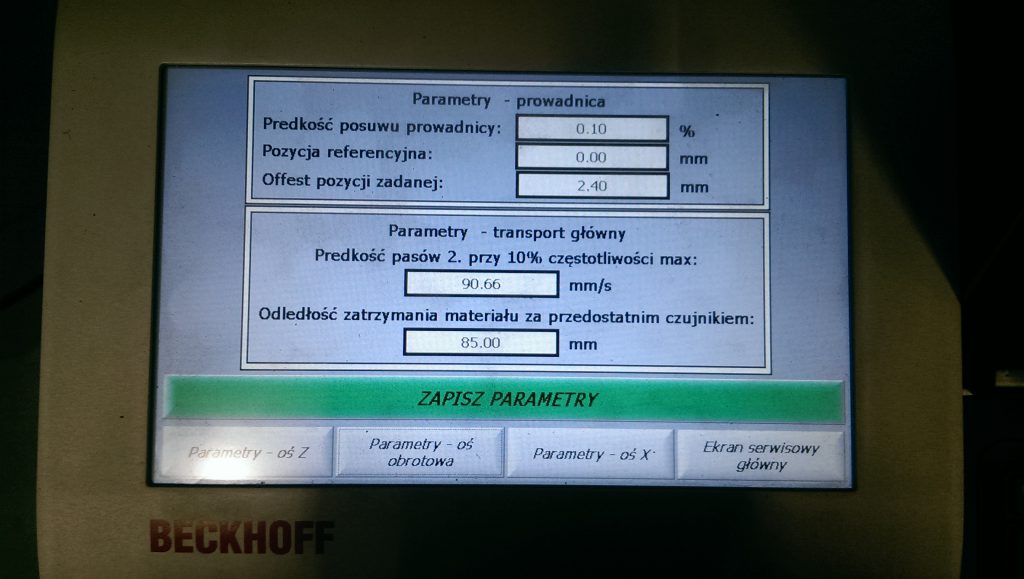
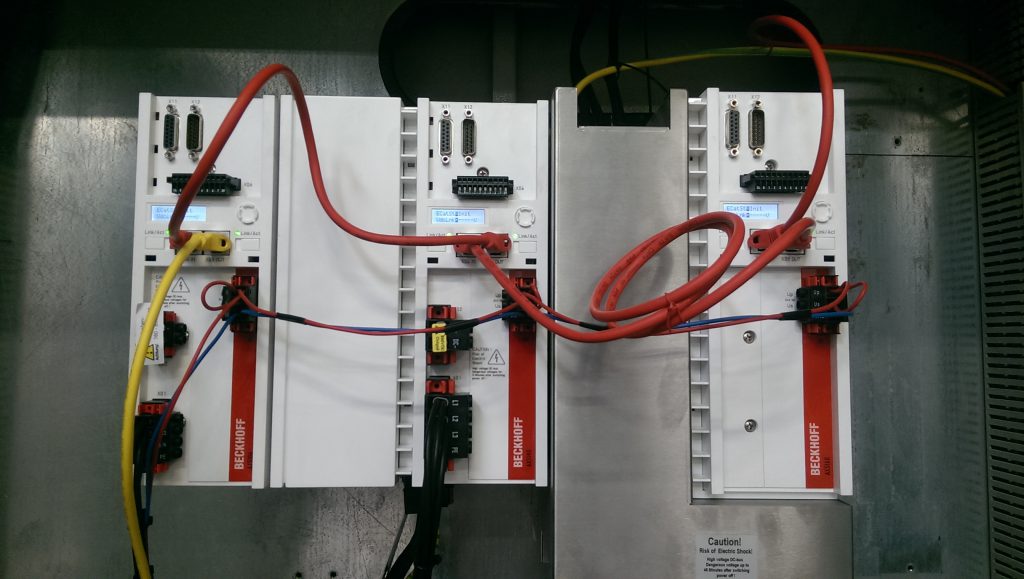
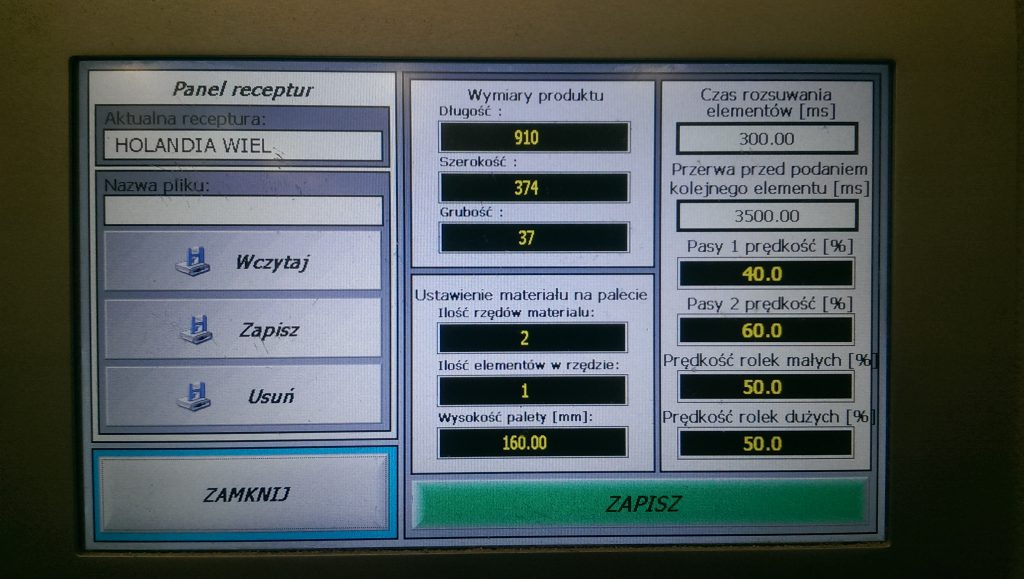
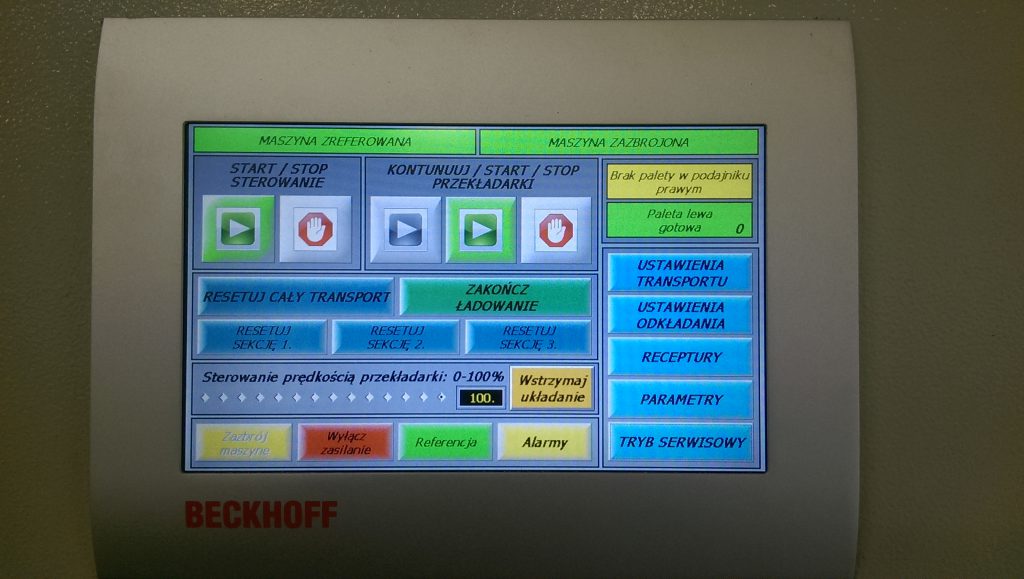
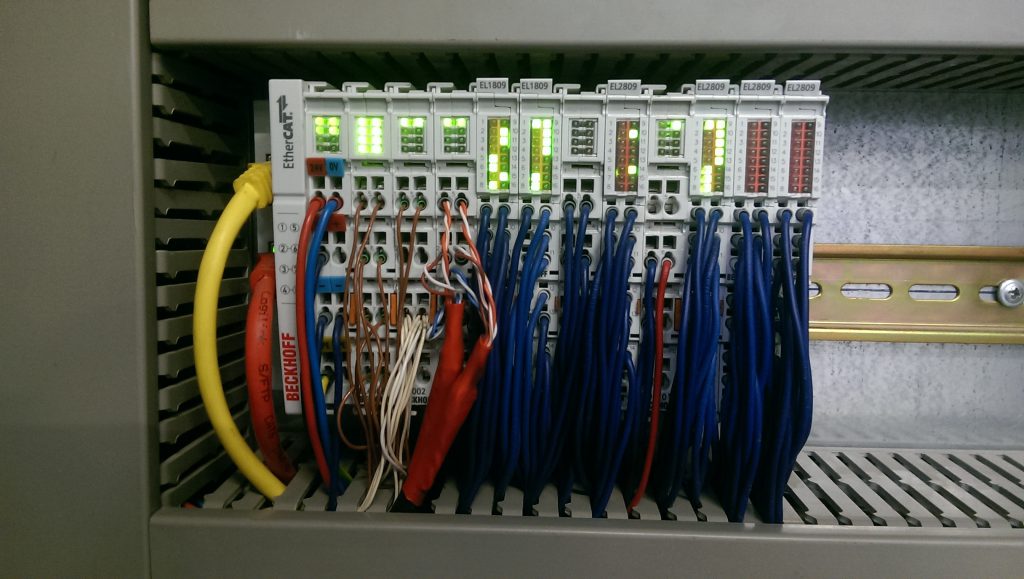
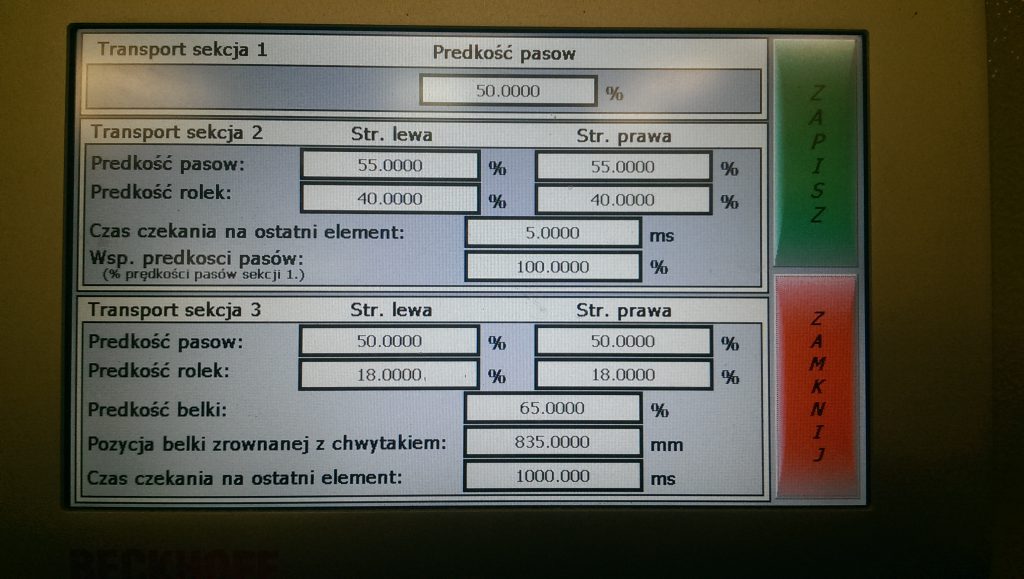
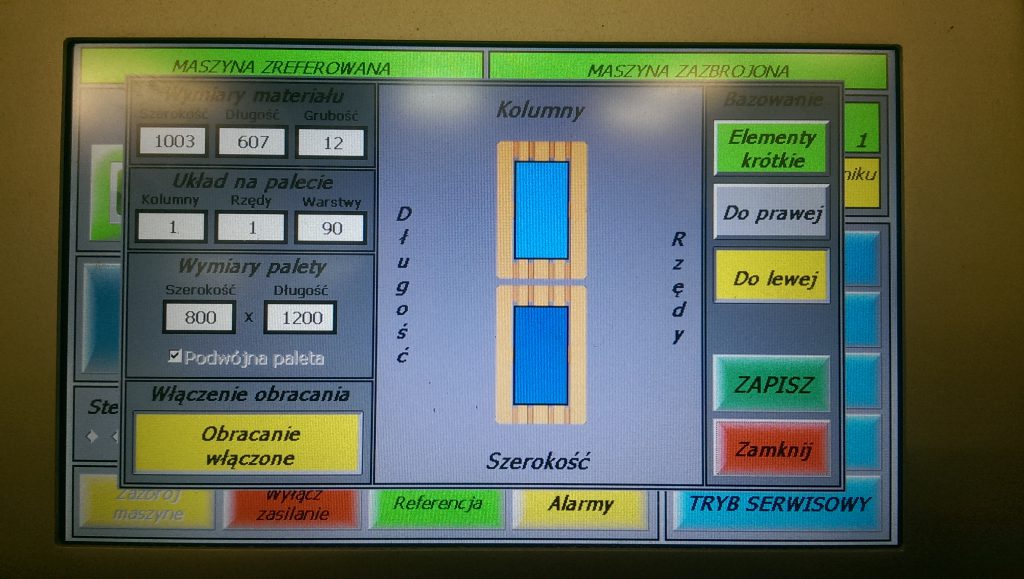
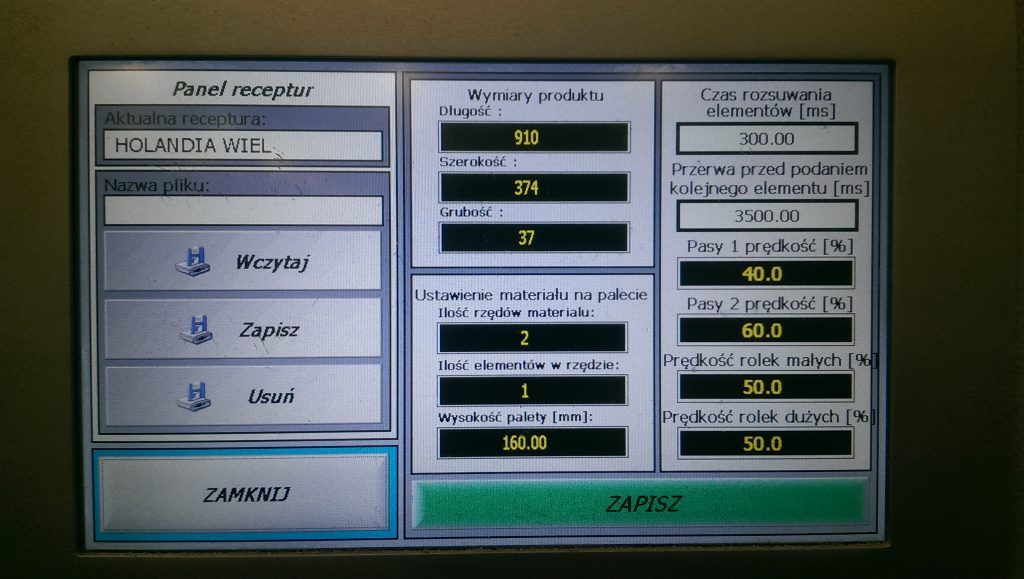
- 3-osiowy manipulator realizujący funkcje podawania materiału na linię produkcyjną.
- Wózek odbierający puste palety.
- Dwie komory pełniące funkcje zasobników materiału.
- Dobrać odpowiednie elementy automatyki.
- Przeprowadzić prace elektryczne przy montażu nowego sterownika oraz dodatkowych urządzeń wykonawczych.
- Przełączyć wszystkie sygnały do nowego systemu sterowania.
- Wykonać sterowanie w oparciu o funkcje NC oraz napisać program PLC przywracający maszynie wszystkie funkcje, które posiadała pierwotnie.
- Przeprowadzić uruchomienie oraz testy nowego układu sterowania.
- Przygotować przejrzystą i intuicyjną aplikację HMI do sterowania całą maszyną.
- Zmodernizować sterowanie transportu pomiędzy portalem załadunkowym a pierwszą stacją obróbczą.
- Przeszkolić zespół operatorów pracujących na modernizowanej linii.
- Zapewnić wsparcie działu UR w czasie użytkowania maszyny przez klienta.
Nowe sterowanie zrealizowano na urządzeniach firmy BECKHOFF. W skład nowego układu sterowania wszedł panel z ekranem dotykowym, odpowiednie moduły pozwalające na akwizycję danych z obiektu oraz sterowanie urządzeniami wykonawczymi. Maszyna była wyposażona w trzy osie napędzane z użyciem silników serwo, dlatego w układzie sterowania użyte zostały seronapędy AX5000, które pozwalają na obsługę tego typu silników. Stworzono program PLC, który obsługuje całą sekwencję załadunku materiału z dwóch zasobników na stół transportowy. Napisany program steruje również odpowiednim podawaniem materiału na kolejny fragment linii produkcyjnej, załadunkiem materiału do komór oraz wózkiem odbierającym puste palety.
Sterowanie transportem:Po modernizacji sterowania transport odpowiednio bazował materiał anastępnie podawał go na stację obróbczą. Ponieważ cały transport składał się z kilku sekcji udało się zrealizować na nim również funkcję bufora materiału. Operator dostał możliwość regulowania prędkości każdej z sekcji transportu oraz zmian parametrów odpowiedzialnych za odpowiednie podawanie materiału do stacji obróbczej.
Aplikacja HMI:Wizualizacje napisano w środowisku InduSoft Web Studio, które jest w pełni zgodne ze standardami systemów klasy SCADA. Umożliwia ono tworzenie ekranów synoptycznych, ekranów zawierających aktywne elementy służące do sterowania maszyną, obsługę alarmów, archiwizację zamiennych procesowych oraz łatwe rozwijanie tworzonych aplikacji. Zastosowano system zarządzania użytkownikami w celu zabezpieczenia parametrów pracy przed ich zmianą przez osoby nieupoważnione. W celu ułatwienia operatorom szybkiej diagnozy awarii do aplikacji dodano moduł obsługi ostrzeżeń i alarmów. Aplikacja pozwala również na zapamiętywanie zestawów parametrów, co pozwala na bardzo szybkie przestawienie jej na pracę z materiałem o innych parametrach.
Dostęp zdalny:Aby maksymalnie skrócić czas reakcji serwisu na awarię, przygotowane zostało połączenie internetowe pozwalające na zdalną diagnostykę maszyny. Połączenie zdalne pozwala również na wprowadzanie zmian w programie sterującym.
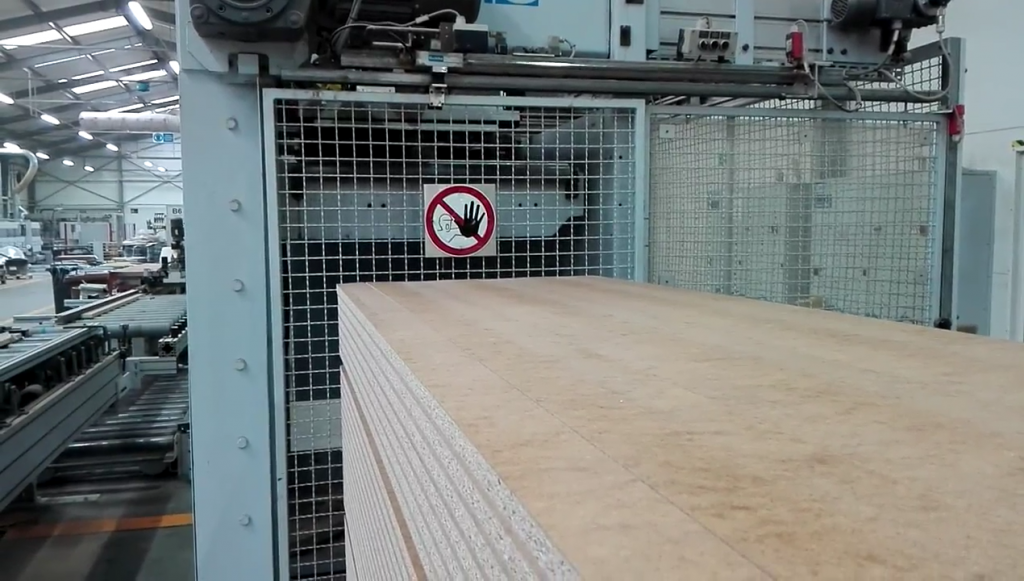
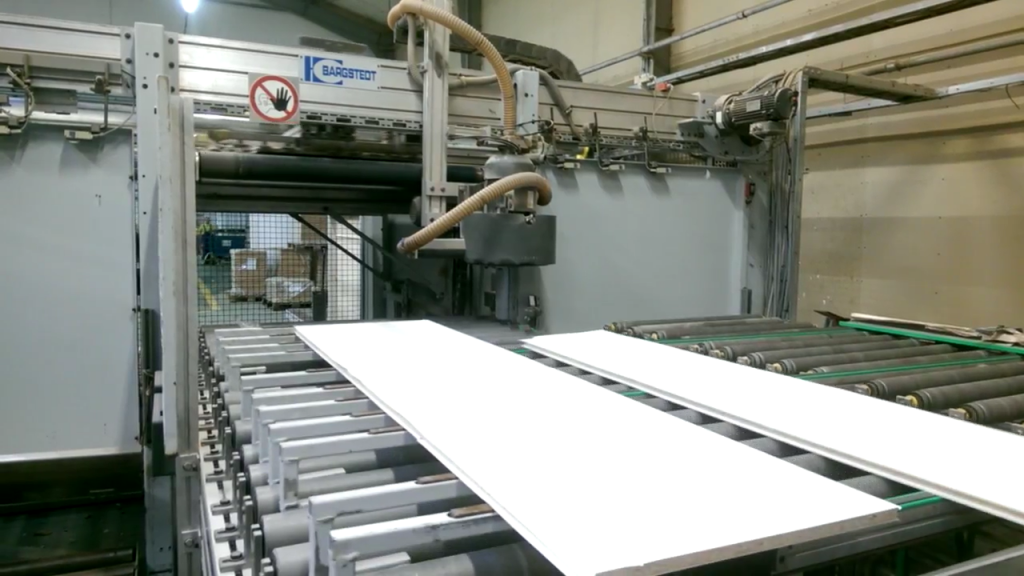
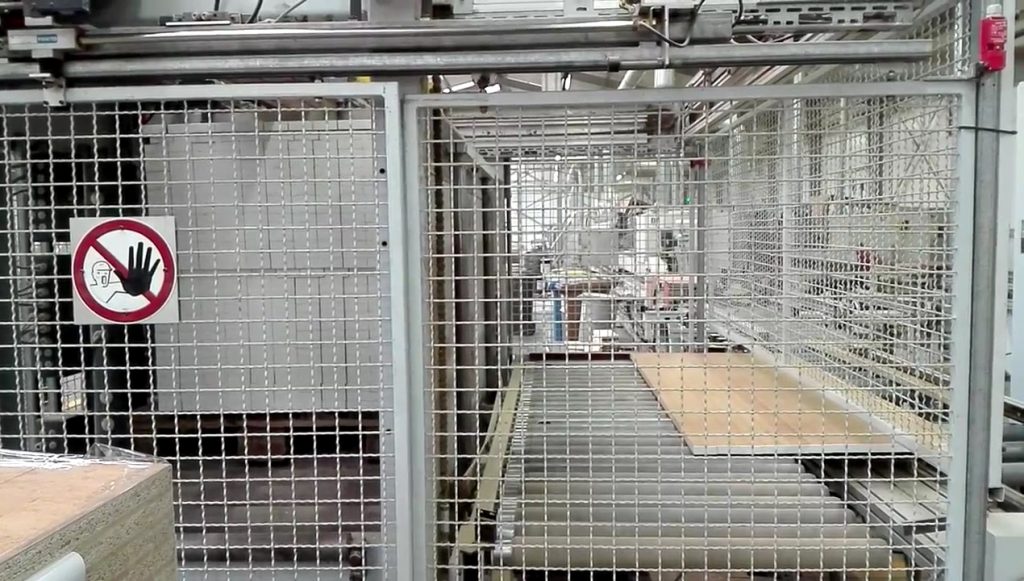
- 2-osiowy manipulator realizujący funkcje podawania materiału na linię produkcyjną.
- Wózek odbierający puste palety.
- Jedna lub dwie komory pełniące funkcje zasobników materiału.
- Dobrać odpowiednie elementy automatyki.
- Przeprowadzić prace elektryczne przy montażu nowego sterownika oraz dodatkowych urządzeń wykonawczych.
- Przełączyć wszystkie sygnały do nowego systemu sterowania.
- Zrealizować sterowanie w oparciu o funkcje NC oraz napisać program PLC przywracający maszynie wszystkie funkcje, które posiadała pierwotnie.
- Przeprowadzić uruchomienie oraz testy nowego układu sterowania.
- Wykonać przejrzystą i intuicyjną aplikację HMI do sterowania całą maszyną.
- Zmodernizować sterowanie transportu pomiędzy portalem załadunkowym a pierwszą stacją obróbczą.
- Przeszkolić zespół operatorów pracujących na modernizowanej linii.
- Zapewnić wsparcie działu UR w czasie użytkowania maszyny przez klienta.
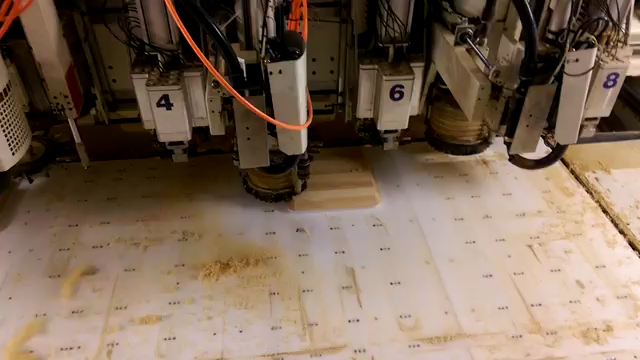
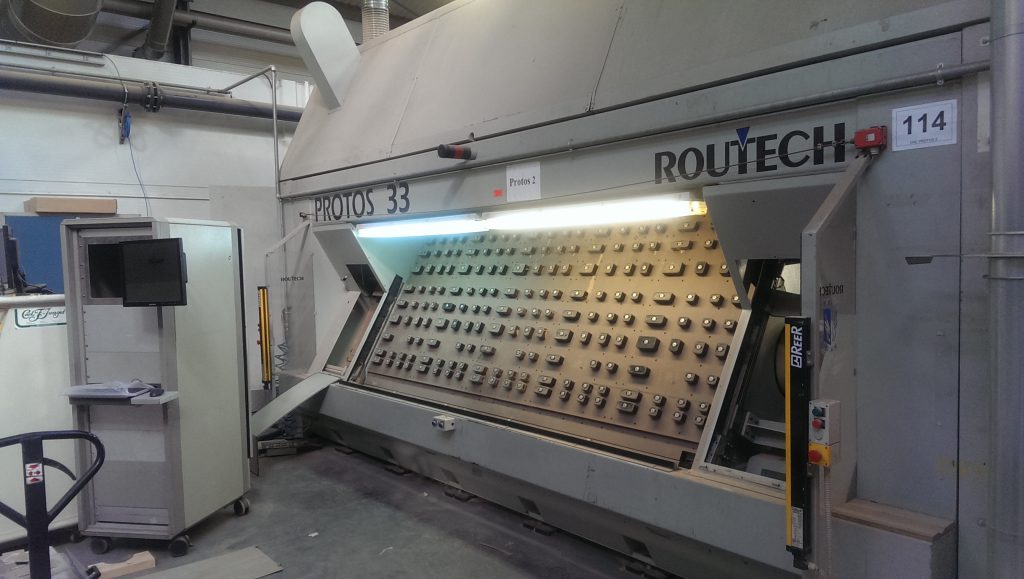
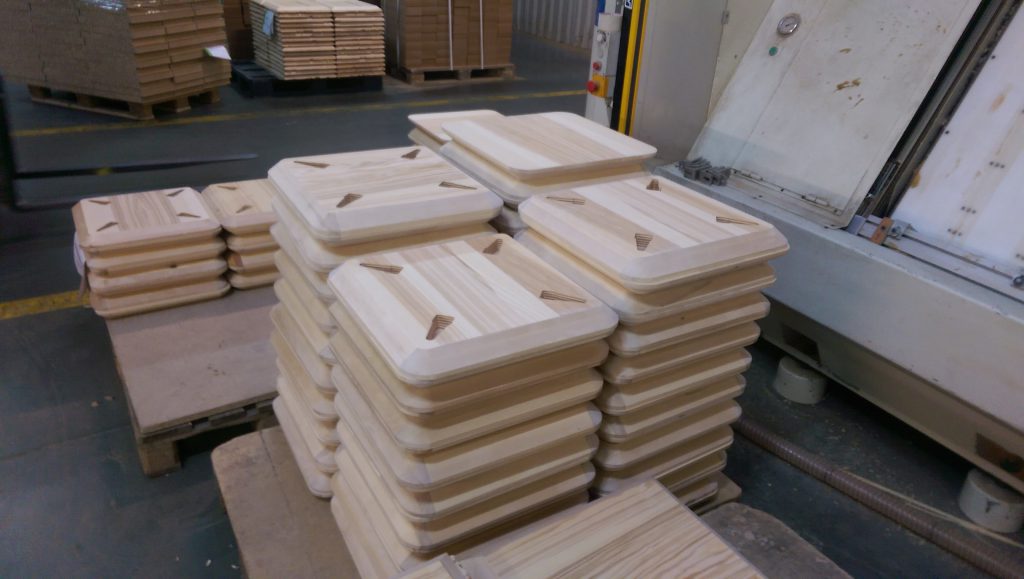
W ramach modernizacji należało:
- Dobrać odpowiednie elementy automatyki.
- Przeprowadzić prace elektryczne przy montażu nowego sterownika oraz dodatkowych urządzeń wykonawczych.
- Przełączyć wszystkie sygnały do nowego systemu sterowania.
- Uruchomić sterowanie CNC.
- Przeprowadzić uruchomienie maszyny oraz testy nowego układu sterowania.
- Skonfigurować aplikację HMI do sterowania całą maszyną.
- Przeszkolić zespół operatorów pracujących na modernizowanej linii.
- Zapewnić wsparcie działu UR w czasie użytkowania maszyny przez klienta.
Nowe sterowania zrealizowano na urządzeniach oraz oprogramowaniu firmy BECKHOFF. W skład nowych układów sterowania weszły komputery przemysłowe, odpowiednie moduły pozwalające na akwizycję danych z obiektów oraz sterowanie urządzeniami wykonawczymi.
Urządzenia napędowe zostały przeprogramowane tak aby współpracowały z nowymi układami sterowania. Zainstalowano, sparametryzowano i przetestowano oprogramowanie CNC, które pozwala na obsługę maszyn poprzez program w języku G-code. Istnieje również możliwość sterowania napędami za pomocą kółka ręcznego.
Wsparcie klienta:Aby maksymalnie skrócić czas reakcji serwisu na awarię, przygotowane zostało połączenie internetowe pozwalające na zdalną diagnostykę maszyn. Połączenie zdalne pozwala również na wprowadzanie zmian w programach sterujących.
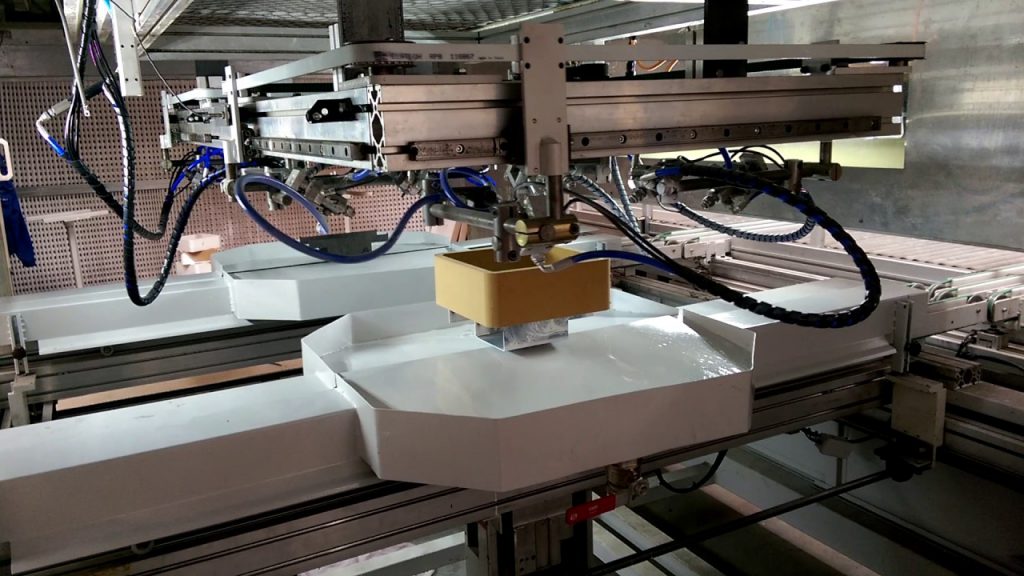
W ramach modernizacji należało:
- Dobrać odpowiednie elementy automatyki.
- Przeprowadzić prace elektryczne przy montażu nowego sterownika oraz dodatkowych urządzeń wykonawczych.
- Przełączyć wszystkie sygnały do nowego systemu sterowania.
- Stworzyć sterowanie w oparciu o funkcje NC oraz napisać program PLC przywracający maszynie wszystkie funkcje, które posiadała pierwotnie.
- Przeprowadzić uruchomienie oraz testy nowego układu sterowania.
- Stworzyć przejrzystą i intuicyjną aplikację HMI do sterowania stanowiskami.
- Przeszkolić zespół operatorów pracujących na modernizowanej linii.
- Zapewnić wsparcie działu UR w czasie użytkowania maszyny przez klienta.
Sterowanie stanowiska podcinania elementów Nowe sterowanie zrealizowano na urządzeniach firmy BECKHOFF. W skład nowego układu sterowania wszedł panel z ekranem dotykowym, odpowiednie moduły pozwalające na akwizycję danych z obiektu oraz sterowanie urządzeniami wykonawczymi. Sterowanie zrealizowano w oparciu o funkcje NC i sterowanie analogowe. Stworzono program PLC, który obsługuje sekwencję podania i bazowania elementu, malowania zgodnie z wprowadzonymi parametrami oraz wyjazd gotowego elementu poza komorę lakierniczą.
Aplikacja HMI:Program wizualizacji HMI wykonano w środowisku InduSoft Web Studio, które jest w pełni zgodne ze standardami systemów klasy SCADA. Umożliwia ono tworzenie ekranów synoptycznych, ekranów zawierających aktywne elementy służące do sterowania maszyną, obsługę alarmów, archiwizację zamiennych procesowych oraz łatwe rozwijanie tworzonych aplikacji. Zastosowano system zarządzania użytkownikami w celu zabezpieczenia parametrów pracy przed ich zmianą przez osoby nieupoważnione. W celu ułatwienia operatorom szybkiej diagnozy awarii do aplikacji dodano moduł obsługi ostrzeżeń i alarmów. Aplikacja pozwala również na zapamiętywanie zestawów parametrów, co pozwala na bardzo szybkie przestawienie jej na pracę z materiałem o innych wymiarach.
Dostęp zdalnyAby maksymalnie skrócić czas reakcji serwisu na awarię, przygotowane zostało połączenie internetowe pozwalające na zdalną diagnostykę maszyny. Połączenie zdalne pozwala również na wprowadzanie zmian w programie sterującym.

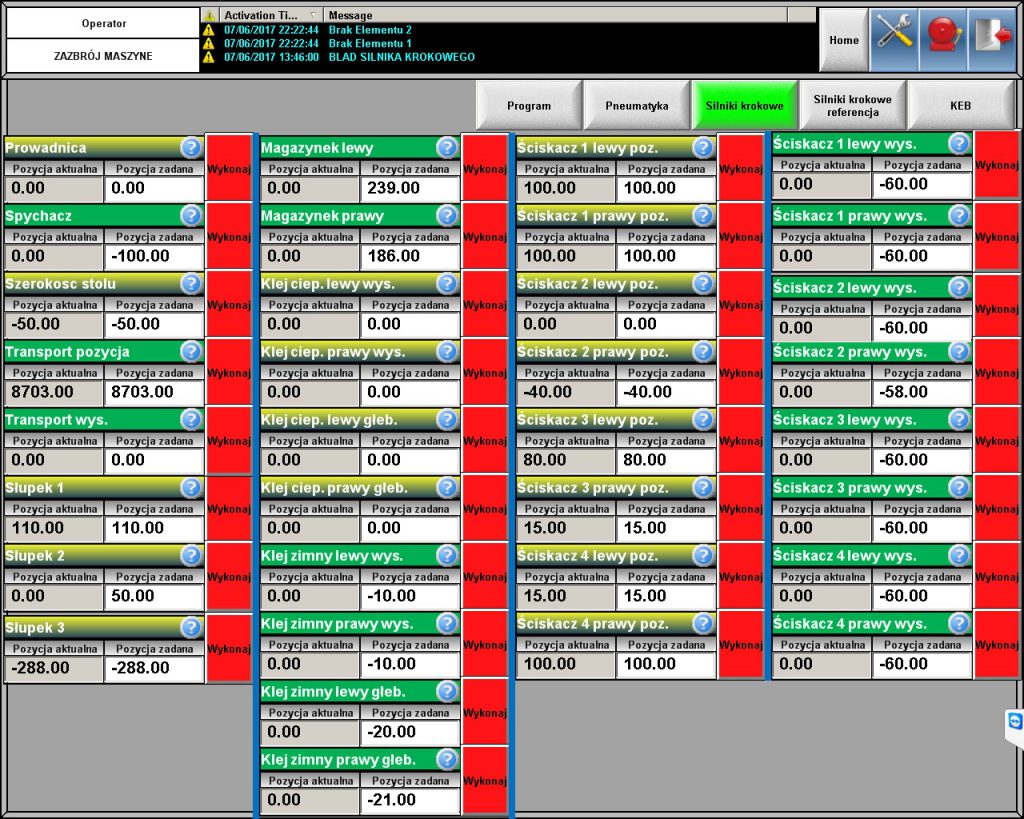
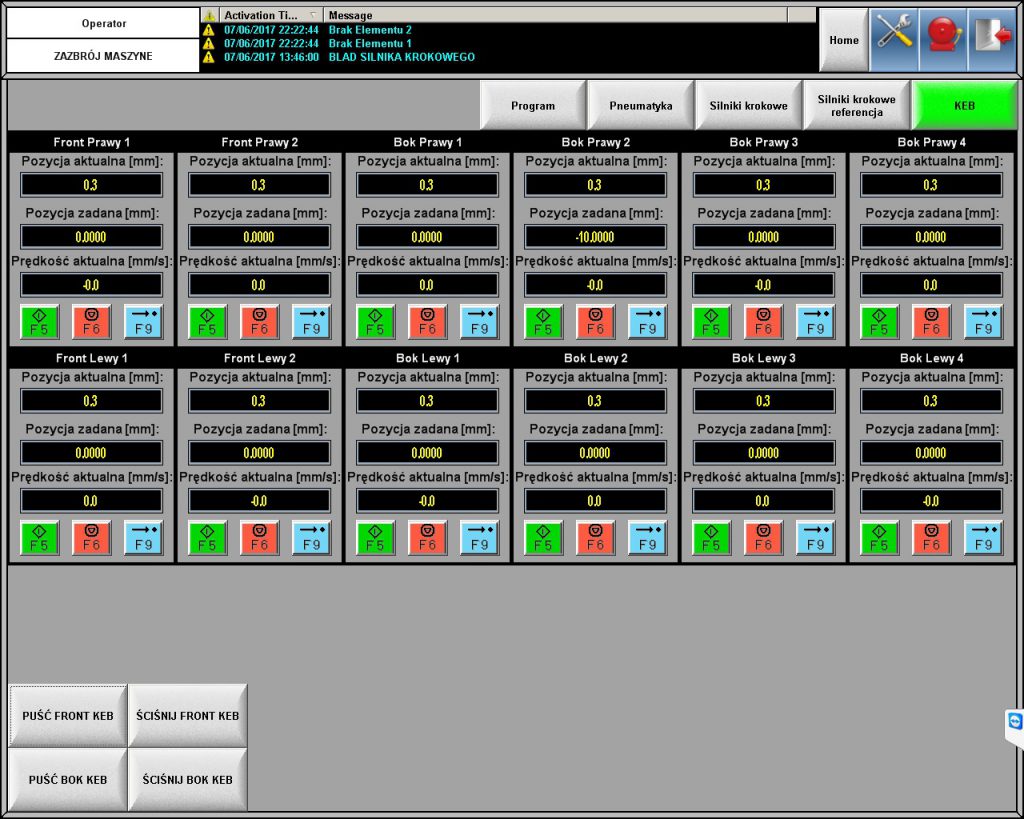
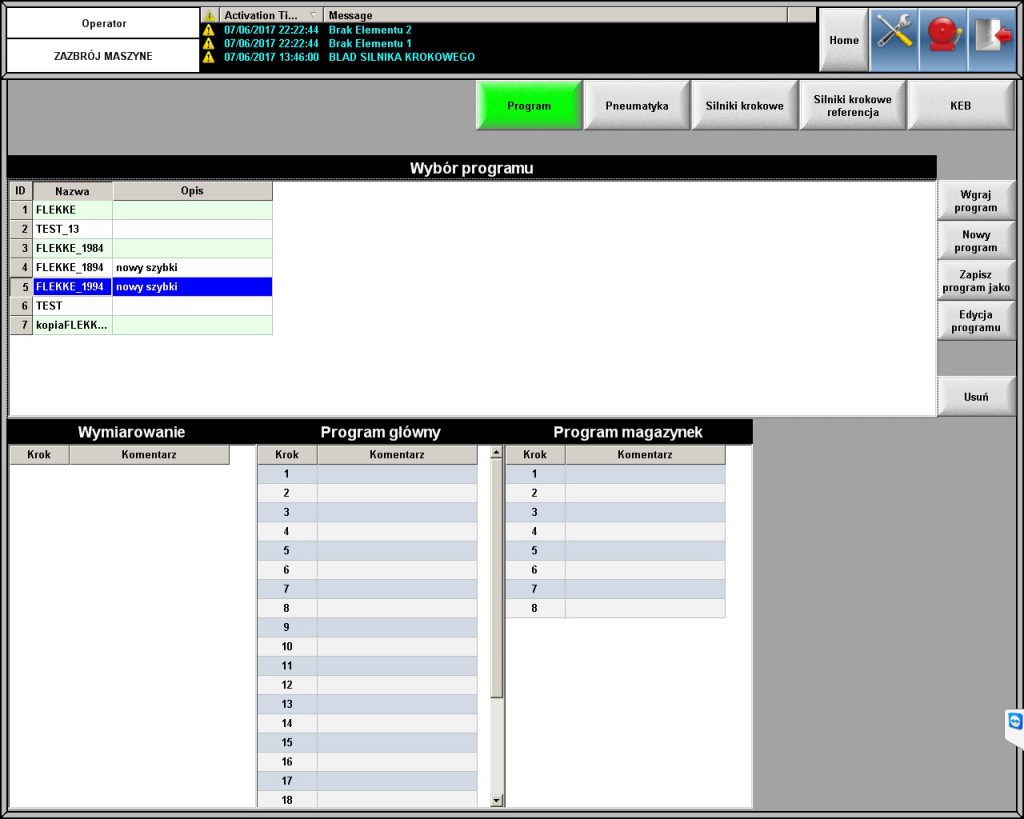
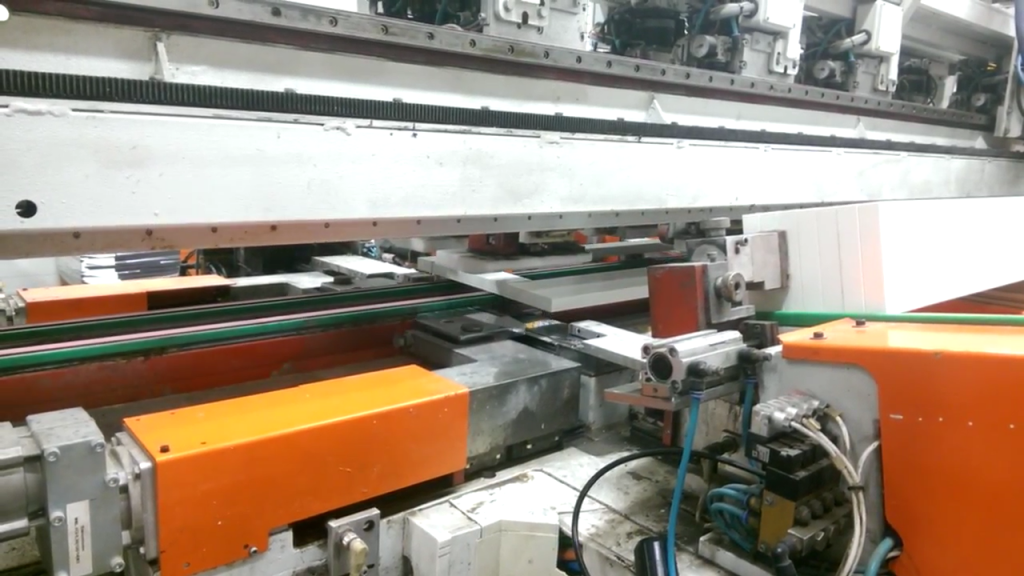
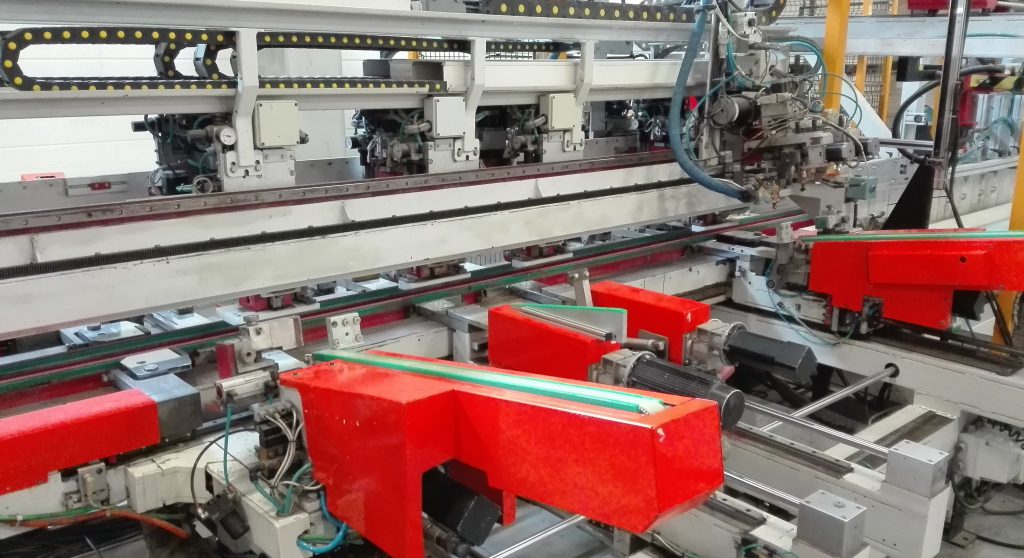
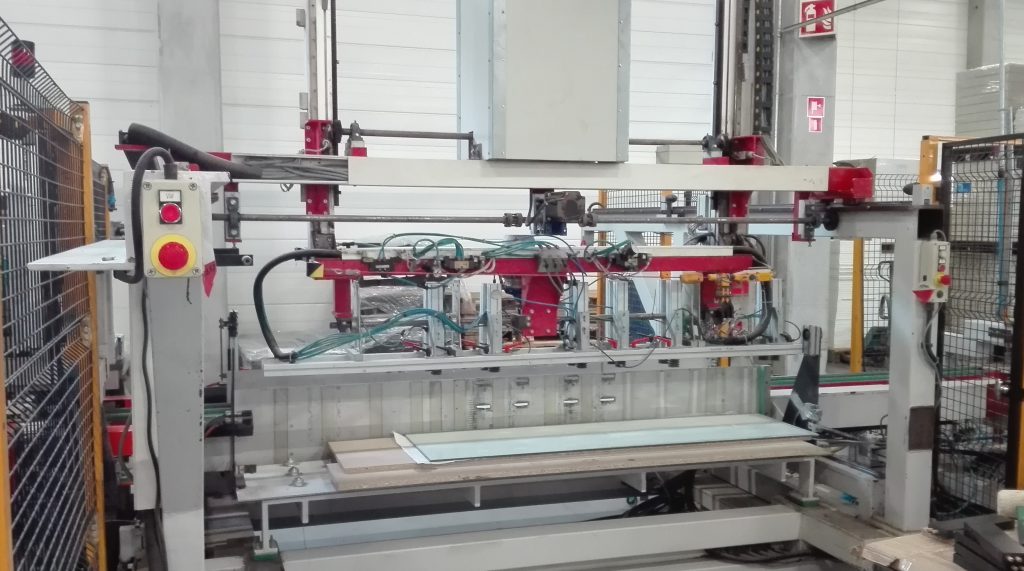
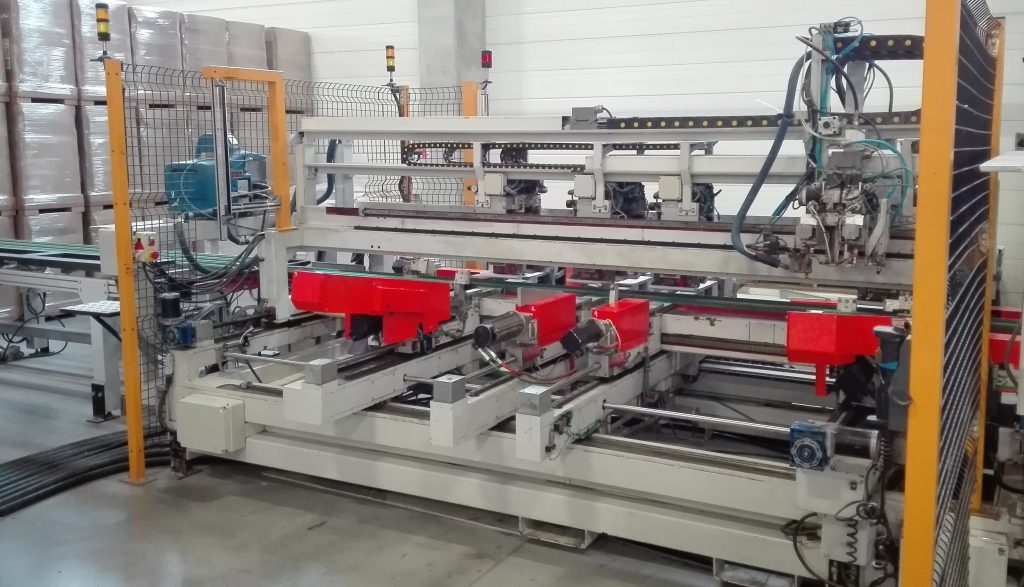
W ramach projektu:
- Napisano program PLC sterujący przebiegiem programów stworzonych przez technologów.
- Skomunikowano się i uruchomiono urządzenia wykonawcze pierwotnie zamontowane na linii, między innymi:
- a) sterowniki silników krokowych SAIA
- b) serwonapędy KEB
- c) falowniki KEB
- Przeprowadzono uruchomienie oraz testy działania linii.
- Napisano przejrzystą i intuicyjną aplikację HMI do sterowania stanowiskami.
- Przeprowadzić uruchomienie oraz testy nowego układu sterowania.
- Przeszkolono pracowników, którzy mieli pracować na modernizowanej linii.
- Zapewniono wsparcie klienta w czasie użytkowania linii.
Program PLC przygotowany na stacji głównej, został przygotowany zgodnie z wymaganymi przez maszyne krokami. Maszyna potrafiła pobierać wszystkie potrzebne elementy z magazynków zamontowanych przy transporterze, następnie odpowiednio je pozycjonowała i ściskała tworząc gotowy produkt. Jeżeli proces produkcji wymagał klejenia elementów, klejem zimnym lub gorącym, maszyna przed zaciśnięciem ramki wprowadzała klej w przygotowane otwory. Cały proces produkcji, od pobrania półfabrykatów aż do wyjazdu gotowego produktu, przebiegał automatycznie.
Aplikację HMI wykonano w środowisku InduSoft Web Studio, które jest w pełni zgodne ze standardami systemów klasy SCADA. Umożliwia ono tworzenie ekranów synoptycznych, ekranów zawierających aktywne elementy służące do sterowania maszyną, obsługę alarmów, archiwizację zamiennych procesowych oraz łatwe rozwijanie tworzonych aplikacji. Zastosowano system zarządzania użytkownikami w celu zabezpieczenia zaawansowanych parametrów pracy przed ich zmianą przez osoby nieupoważnione. W celu ułatwienia operatorom szybkiej diagnozy awarii do aplikacji dodano moduł obsługi ostrzeżeń i alarmów. Programy stworzone przez technologów wraz z komentarzami były przechowywane w bazie danych zainstalowanej na tym samym komputerze. Obsługa programów, czyli tworzenie, przeglądanie, modyfikacja i wysyłanie ich do sterownika PLC, była prowadzona z głównego komputera.
Aby maksymalnie skrócić czas reakcji serwisu na awarię, przygotowane zostało połączenie internetowe pozwalające na zdalną diagnostykę linii. Połączenie zdalne pozwala również na wprowadzanie zmian w programie sterującym.
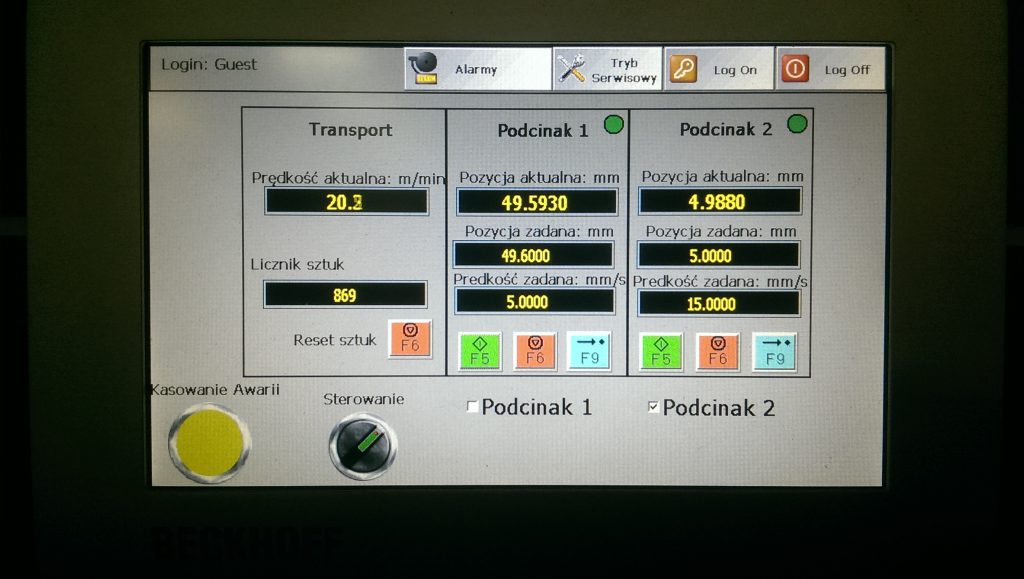
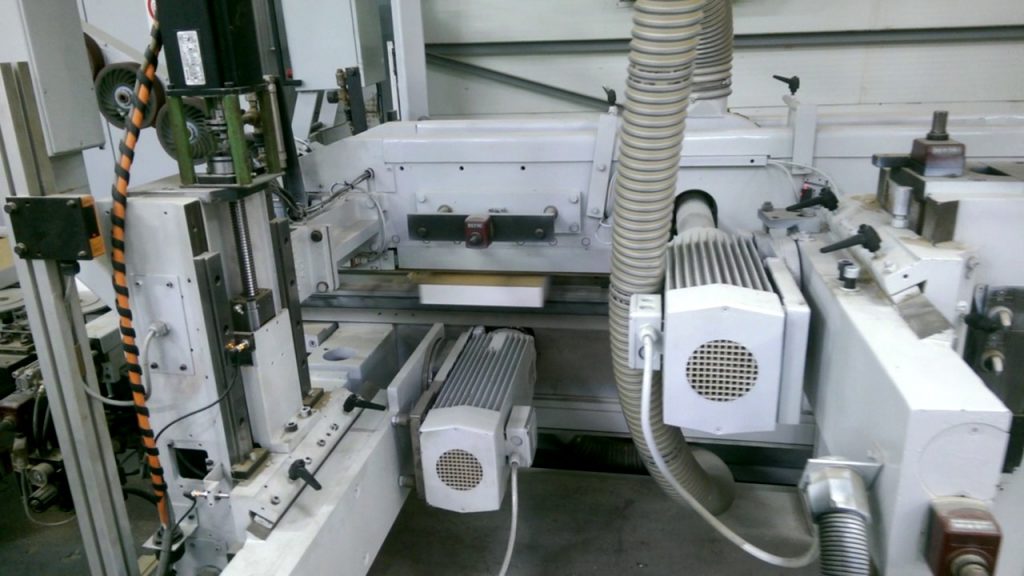
W ramach modernizacji należało: Dobrać odpowiednie elementy automatyki. Przeprowadzić prace elektryczne przy montażu nowego sterownika oraz dodatkowych urządzeń wykonawczych. Przełączyć wszystkie sygnały do nowego systemu sterowania. Stworzyć sterowanie w oparciu o funkcje NC oraz napisać program PLC przywracający maszynie wszystkie funkcje, które posiadała pierwotnie. Przeprowadzić uruchomienie oraz testy nowego układu sterowania. Stworzyć przejrzystą i intuicyjną aplikację HMI do sterowania stanowiskami. Przeszkolić zespół operatorów pracujących na modernizowanej linii. Zapewnić wsparcie działu UR w czasie użytkowania maszyny przez klienta.
- Sterowanie stanowiska podcinania elementów
- Nowe sterowanie zrealizowano na urządzeniach firmy BECKHOFF oraz ABB.
- W skład nowego układu sterowania wszedł panel z ekranem dotykowym, odpowiednie moduły pozwalające na akwizycję danych z obiektu oraz sterowanie urządzeniami wykonawczymi.
- Do napędu rolki podającej okleinę użyto serwowzmacniaczy oraz serwosilników BECKHOFF. Dzięki zastosowaniu wymienionego wyżej sprzętu, udało się osiągnąć dokładność na poziomie 1 mm przy podawaniu okleiny z prędkością 30 m/min.
- Stworzono program PLC, który obsługuje sekwencję podawania okleiny zgodnie z wprowadzonymi parametrami.
Aplikację HMI wykonano w środowisku InduSoft Web Studio, które jest w pełni zgodne ze standardami systemów klasy SCADA. Umożliwia ono tworzenie ekranów synoptycznych, ekranów zawierających aktywne elementy służące do sterowania maszyną, obsługę alarmów, archiwizację zamiennych procesowych oraz łatwe rozwijanie tworzonych aplikacji.
Zastosowano system zarządzania użytkownikami w celu zabezpieczenia parametrów pracy przed ich zmianą przez osoby nieupoważnione. W celu ułatwienia operatorom szybkiej diagnozy awarii do aplikacji dodano moduł obsługi ostrzeżeń i alarmów.
Aplikacja pozwala również na zapamiętywanie zestawów parametrów, co pozwala na bardzo szybkie przestawienie jej na pracę z materiałem o innych wymiarach.
Aby maksymalnie skrócić czas reakcji serwisu na awarię, przygotowane zostało połączenie internetowe pozwalające na zdalną diagnostykę maszyny. Połączenie zdalne pozwala również na wprowadzanie zmian w programie sterującym.
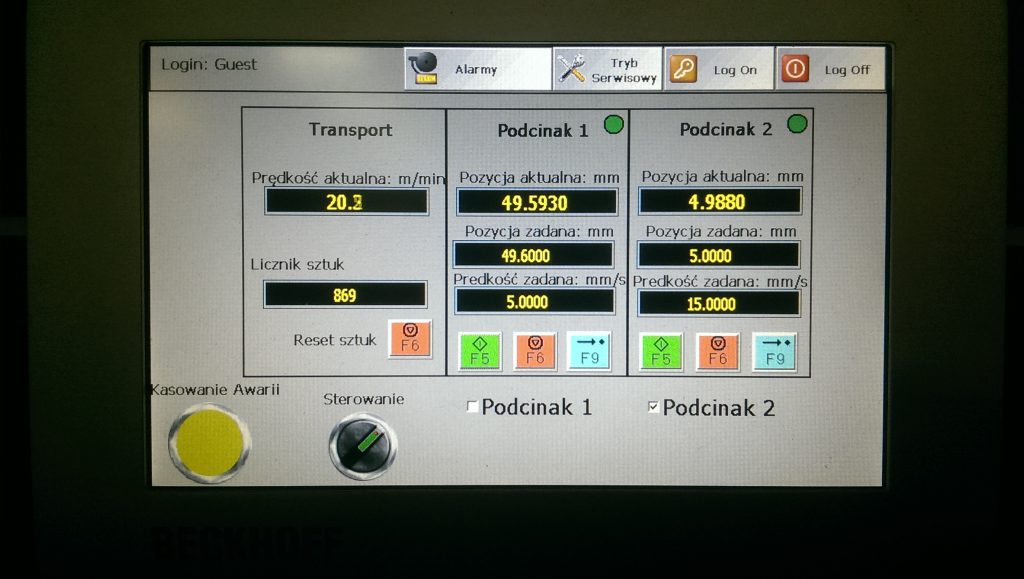
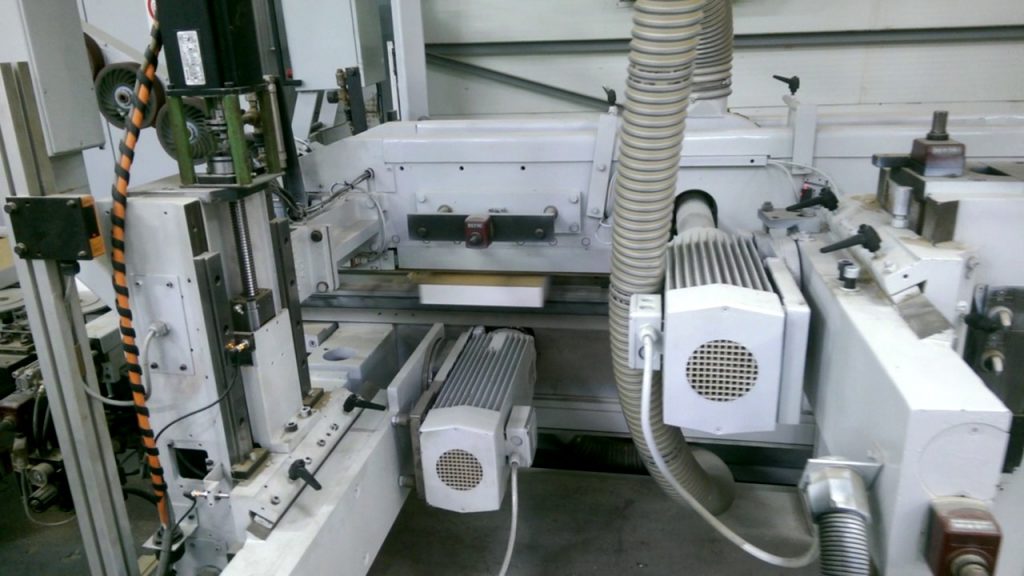
W ramach modernizacji należało:
- Dobrać odpowiednie elementy automatyki.
- Przeprowadzić prace elektryczne przy montażu nowego sterownika oraz dodatkowych urządzeń wykonawczych.
- Przełączyć wszystkie sygnały do nowego systemu sterowania.
- Stworzyć sterowanie w oparciu o funkcje NC oraz napisać program PLC przywracający maszynie wszystkie funkcje, które posiadała pierwotnie.
- Przeprowadzić uruchomienie oraz testy nowego układu sterowania.
- Stworzyć przejrzystą i intuicyjną aplikację HMI do sterowania całą maszyną.
- Zmodernizować sterowanie transportu pomiędzy portalem załadunkowym a pierwszą stacją obróbczą.
- Przeszkolić zespół operatorów pracujących na modernizowanej linii.
- Zapewnić wsparcie działu UR w czasie użytkowania maszyny przez klienta.
Sterowanie stanowiska podcinania elementów Nowe sterowanie zrealizowano na urządzeniach firmy BECKHOFF. W skład nowego układu sterowania wszedł panel z ekranem dotykowym, odpowiednie moduły pozwalające na akwizycję danych z obiektu oraz sterowanie urządzeniami wykonawczymi.
Do napędu osi unoszącej piły użyto serwowzmacniaczy oraz serwosilników INDRAMAT, zostały one odpowiednio zaprogramowane aby pracowały sterowane przez nowy sterownik PLC. Napędy te sterowane były sygnałami analogowymi, co pozwoliło na płynne i dokładne panowanie nad ich ruchami. Stworzono program PLC, który obsługuje sekwencję podcinania materiału zgodnie z wprowadzonymi przez operatora parametrami.
Aplikację HMI stworzono w środowisku InduSoft Web Studio, które jest w pełni zgodne ze standardami systemów klasy SCADA. Umożliwia ono tworzenie ekranów synoptycznych, ekranów zawierających aktywne elementy służące do sterowania maszyną, obsługę alarmów, archiwizację zamiennych procesowych oraz łatwe rozwijanie tworzonych aplikacji.
Zastosowano system zarządzania użytkownikami w celu zabezpieczenia parametrów pracy przed ich zmianą przez osoby nieupoważnione. W celu ułatwienia operatorom szybkiej diagnozy awarii do aplikacji dodano moduł obsługi ostrzeżeń i alarmów.
Aplikacja pozwala również na zapamiętywanie zestawów parametrów, co pozwala na bardzo szybkie przestawienie jej na pracę z materiałem o innych wymiarach.
Aby maksymalnie skrócić czas reakcji serwisu na awarię, przygotowane zostało połączenie internetowe pozwalające na zdalną diagnostykę maszyny. Połączenie zdalne pozwala również na wprowadzanie zmian w programie sterującym.
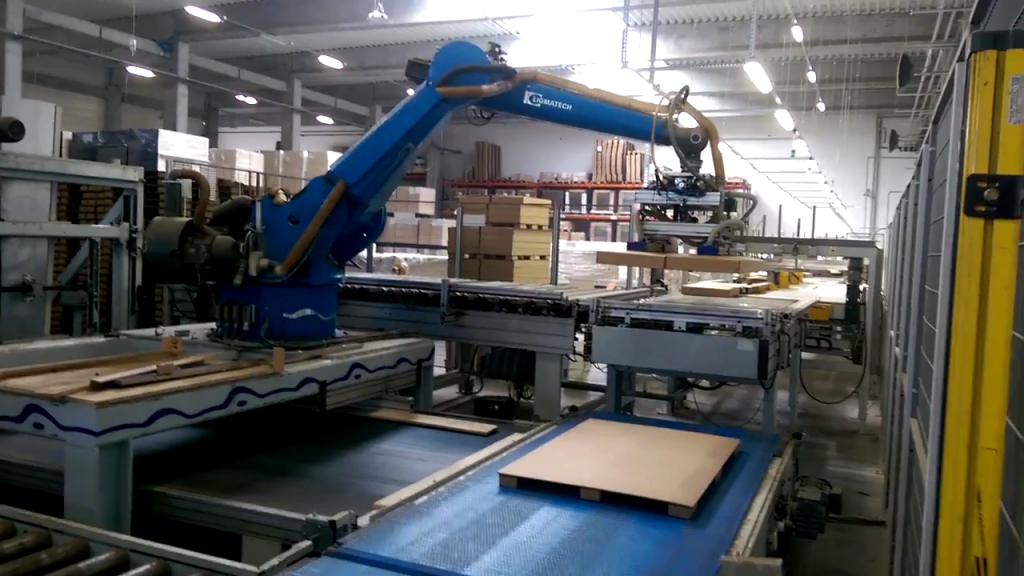
W ramach modernizacji należało:
- Dobrać odpowiednie elementy automatyki.
- Przeprowadzić prace elektryczne przy montażu nowego sterownika oraz dodatkowych urządzeń wykonawczych.
- Przełączyć wszystkie sygnały do nowego systemu sterowania.
- Stworzyć sterowanie w oparciu o funkcje NC oraz napisać program PLC przywracający maszynie wszystkie funkcje, które posiadała pierwotnie.
- Przeprowadzić uruchomienie oraz testy nowego układu sterowania.
- Stworzyć przejrzystą i intuicyjną aplikację HMI do sterowania całą maszyną.
- Zmodernizować sterowanie transportu pomiędzy portalem załadunkowym a pierwszą stacją obróbczą.
- Przeszkolić zespół operatorów pracujących na modernizowanej linii.
- Zapewnić wsparcie działu UR w czasie użytkowania maszyny przez klienta.
Sterowanie stanowiska podcinania elementów Nowe sterowanie zrealizowano na urządzeniach firmy BECKHOFF. W skład nowego układu sterowania wszedł panel z ekranem dotykowym, odpowiednie moduły pozwalające na akwizycję danych z obiektu oraz sterowanie urządzeniami wykonawczymi.
Do napędu osi unoszącej piły użyto serwowzmacniaczy oraz serwosilników INDRAMAT, zostały one odpowiednio zaprogramowane aby pracowały sterowane przez nowy sterownik PLC. Napędy te sterowane były sygnałami analogowymi, co pozwoliło na płynne i dokładne panowanie nad ich ruchami. Stworzono program PLC, który obsługuje sekwencję podcinania materiału zgodnie z wprowadzonymi przez operatora parametrami.
Aplikację HMI napisano w środowisku InduSoft Web Studio, które jest w pełni zgodne ze standardami systemów klasy SCADA. Umożliwia ono tworzenie ekranów synoptycznych, ekranów zawierających aktywne elementy służące do sterowania maszyną, obsługę alarmów, archiwizację zamiennych procesowych oraz łatwe rozwijanie tworzonych aplikacji.
Zastosowano system zarządzania użytkownikami w celu zabezpieczenia parametrów pracy przed ich zmianą przez osoby nieupoważnione. W celu ułatwienia operatorom szybkiej diagnozy awarii do aplikacji dodano moduł obsługi ostrzeżeń i alarmów.
Aplikacja pozwala również na zapamiętywanie zestawów parametrów, co pozwala na bardzo szybkie przestawienie jej na pracę z materiałem o innych wymiarach.
Aby maksymalnie skrócić czas reakcji serwisu na awarię, przygotowane zostało połączenie internetowe pozwalające na zdalną diagnostykę maszyny. Połączenie zdalne pozwala również na wprowadzanie zmian w programie sterującym.